Auto Bumper Mould
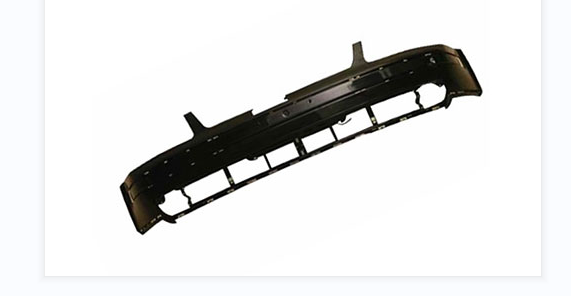
தயாரிப்பு விளக்கம்
The front and rear bumpers of the car are made of plastic, which not only maintains the protection function, but also has the characteristics of harmony and unity with the body shape, lightweight, and low fuel consumption. The plastic front bumper consists of three parts, namely the outer panel, the buffer material, and the cross member. The raw materials of the outer plate and the buffer material are all plastic, the beam is stamped into a U-shaped groove from a cold-rolled sheet, and the thickness of the cold-rolled sheet is about 1.5 mm. There are generally two types of materials used in bumper mold : polyester and polypropylene, and the molding process is generally injection molding.
Automobile Bumper Mold Manufacturing
Green Vitality is a professional automobile mold manufacturer and has rich experience in automobile bumper mold manufacturing.
The car bumper injection moulding designed by Green Vitality not only has the ability to reduce the injury of drivers and passengers during high-speed impact but also has the ability to protect pedestrians. Green Vitality uses an internal parting structure design for the bumper mold. Compared with the traditional outer parting structure design, the inner parting design has higher requirements on the strength of the mold. Correspondingly, the design concept of the bumper mold made by the internal parting structure is more advanced.
Basic Information for Auto Bumper Mould
Auto Bumper Mould Specification
Description Auto Bumper Mold
Plastic material PP
Mould cavity&core steel P20,2738,718H,738H,NAK80,SKD61,E420,etc.
Mould weight (T) 10T
Feeding System Cold runner/ Hot runner
Hot runner brand YUDO, HUSKYFISA, HASCO, MOLD-MASTER
Nos of Cavity 1*1
Manufacture time (day) 120 days
Mould life ≥500000
Packing Vacuum+plywood wooden box
Green Vitality Can Offer You with Auto Bumper Mould
Analysis: Through the analysis of material properties and product feasibility, such as wall thickness, deformation, plastic feeding position, etc., potential problems can be predicted in advance.
Communication: Maintain close communication with customers, and understand the functional requirements and precautions of products from the perspective of customers, such as requirements for weld lines, requirements for appearance, etc.
Design: Strict design review system and checklist check. Before design, during the design of the scheme structure discussion meeting, the designer will check himself according to the checklist; after design, review together with the manufacturing department.
Quality inspection: Quality inspection of each link to discover mass production problems in advance.
Project management: Each project is equipped with a project manager, who strictly follows the schedule to control the project cycle, and provides weekly progress reports and mold photos for each project so that customers can keep abreast of the status.
Service: From mold design to continuous mass production of products, we provide full life cycle service support.
After-sales service: continuous after-sales follow-up service, proactively providing mass production and processing technical consulting services.
Technical support: In the mass production process, if there is any problem with the mold, technical support will be provided unconditionally.
Why Are Auto Bumpers Made of Plastic Material?
Control costs
The bumper steel plate is replaced with plastic, the cost is greatly reduced, the production is convenient, and the plastic bumper is also very malleable, which can meet the bumper design requirements of various car models.