LSR Molding
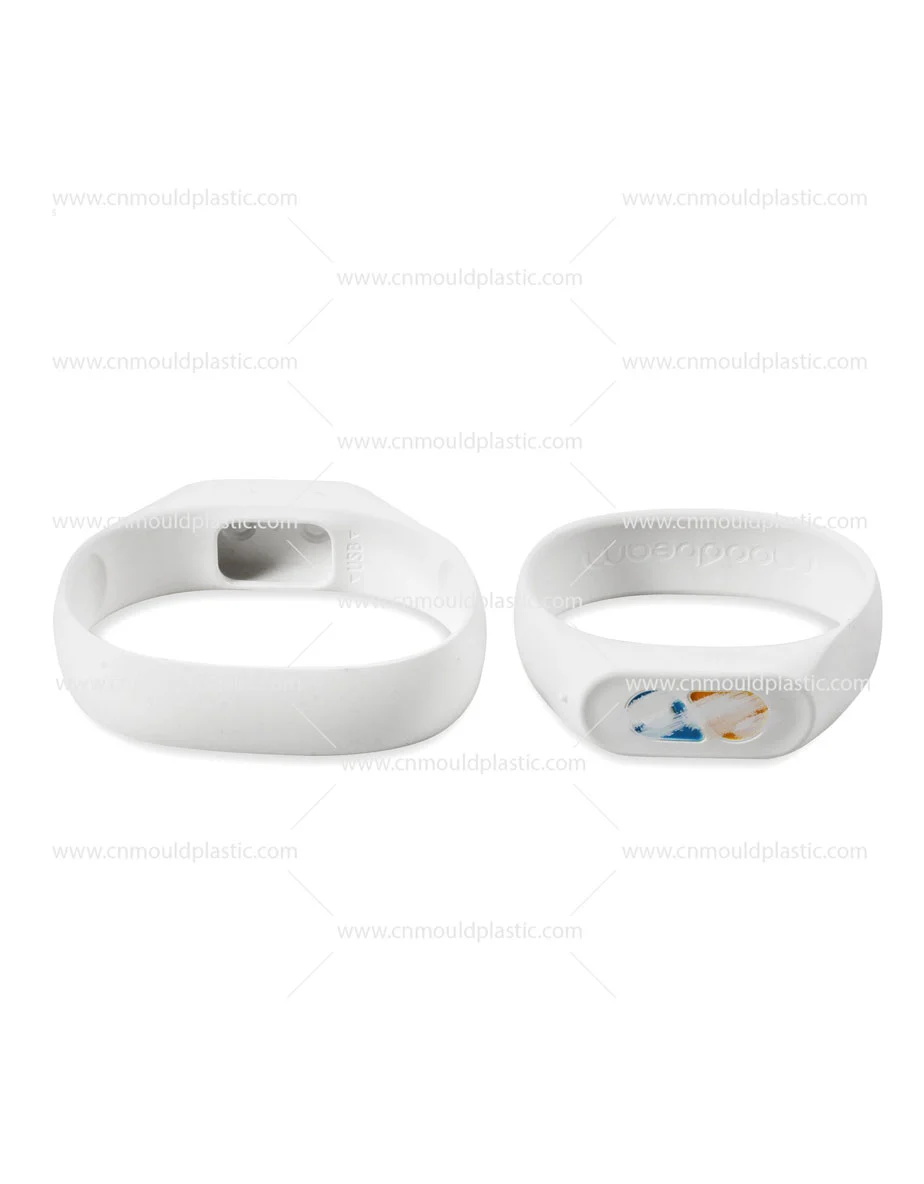
توضیحات محصول
LSR Molding
Liquid Silicone Rubber(LSR) has been in high demand since its development in these days. That's hardly surprising given its physical properties and the variety of applications it may serve. LSR is long-lasting, flexible, stable, and versatile. Customers appreciate the dependability and quality that our company consistently provides, so it's no wonder that our influence in the LSR sector is expanding as well.
Injection moulding of liquid silicone rubber is a process that involves mixing two-part Liquid Silicone Rubber material, then curing it thermally in a mold using a platinum catalyst to produce silicone rubber parts and products.
Liquid Silicone Rubber Molding is quite similar to the traditional process of plastic injection molding. However, the primary distinction between the two methods is that the conveying system for materials is cooled while the mold is heated.
CN: The Perfecting LSR Process
STEP1
Put the base-forming silicone and the platinum catalyst parts of the Liquid Silicone Rubber compounds A & B into the pumping system using the supply drums. Additionally, there is a separate container for the additives and color pigments.
STEP2
Mix the two Liquid Silicone Rubber, base-forming silicone and platinum catalyst by using the metering unit. Make sure that the two Liquid Silicone Rubber are kept at a consistent ratio of 1:1 while being transported simultaneously.
STEP3
Set up and start machine, Inject these mixed compounds into the mold cavity via nozzle and cold runner system.
STEP4
Once the silicone rubber products have undergone vulcanization and solidification, they can be removed from the mold either automatically or manually.
STEP5
The product will be post-processed and inspected.
#APPLICATION
LSR MOLDING Application
Liquid Silicone Rubber is a material that extremely wide applications, suitable for numerous applications in various industries including medical, life sciences, automotive, consumer goods, and industrial products.
Medical & Health: Medical tube, Endoscope components, Breathing face mask, Laryngeal mask;
Automobile: Gasket, O-Ring, Seals, Optical coupling LED lens;
Optics: Exterior and professional Lighting;
Electronics: LED lens, protective cases, Watch bands, Silicone Lightning Cable;
Consumer goods: Earphone, Earplugs, Eyeglass Nose Pads, safety goggles;
Babies & Kids: Silicone baby bottles, Silicone pacifier, Silicone baby toothbrush.
In short, there are numerous products that can be manufactured through the process of liquid silicone molding .
WHY CHOOSE CN LSR Molding
EXTENSIVE EXPERIENCE
For almost 20 years, CN Mould & Plastic Limited has focused on making injection molds and doing injection molding. CN are fully knowledgeable about the LSR molding process and can handle problems that other companies might not be able to handle.
HIGH EFFICIENCY
We are capable of creating prototypes for your parts within a short time frame. This speedy prototyping process enables you to swiftly enhance your parts and commence the production of components promptly.
CUSTOMIZATION
Our team of engineers can assist you in selecting the appropriate type of LSR for your project, producing the products you require. We offer a complete range of services, including mold design, production, assembly, and coordination throughout the entire process.
QUALIFICATIONS
CN has been certified in Quality Management by the International Organization for Standardization (SGS) according to the ISO 9001:2015 and IATF 16949:2016 disciplines.
CRITICAL ADVANTAGES OF
LSR Molding
Advantages of LSR Molding
LSR's versatility and impressive properties make it a valuable material for a wide range of applications. From everyday gadgets to cutting-edge medical devices, LSR is shaping the future in many ways.