HDPE Pipe Production Line
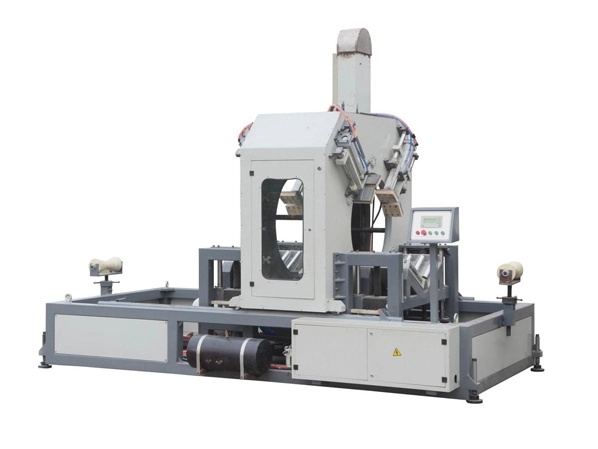
Opis izdelka
HDPE Pipe Production Line
High-Density Polyethylene (HDPE) pipe production line is an advanced manufacturing setup designed for the efficient production of HDPE pipes. HDPE pipes are known for their exceptional durability, flexibility, and corrosion resistance, making them widely used in various industries for transporting fluids and gases.
HDPE tube production line is highly automated and operates continuously to ensure efficiency and precision in manufacturing. It's capable of producing pipes of various sizes and specifications to cater to diverse industrial, agricultural, municipal, and residential needs.
Features of HDPE Pipe Production Line
The machine host extruder using the special treatment single screw extruder, and the forming product is good.
This series HDPE pipe production line is mainly used for producing pipe of water supply and drainage in the field of agriculture and construction, cable and ect.
This HDPE pipe extrusion machine group consist of vacuum calibration tank, haul-off unit, cutting unit, stacker and so on.
The machine units can adopt the single screw co-extruder for extrusion.
The production pipe diameter range: Φ20-Φ2000mm
The extrusion line adopt the electrical system: ABB speed governor, Japanese RKC temperature controller, SIMENS contactor.
HDPE Pipe Production Line Application
HDPE pipe extrusion machines serve various industries and sectors, including:
Water Supply and Distribution: HDPE pipes are widely utilized for water supply networks in municipal, residential, and industrial areas due to their durability, corrosion resistance, and flexibility, making them ideal for transporting potable water over long distances and diverse terrain.
Sewage and Drainage Systems: HDPE pipes are commonly used in sewage and drainage systems because of their resistance to chemicals, abrasion, and corrosion. They effectively convey wastewater, stormwater, and sewage to treatment plants or disposal sites, contributing to efficient waste management.
Gas Distribution: HDPE pipes find extensive use in distributing natural gas and other combustible gases in residential, commercial, and industrial settings. Their lightweight design, ease of installation, and corrosion resistance make them a preferred choice for gas distribution networks.
Irrigation and Agriculture: HDPE pipes are employed in irrigation systems for agricultural purposes, including crop irrigation, drip irrigation, and sprinkler systems. Their flexibility, durability, and UV resistance enable them to withstand harsh outdoor conditions and facilitate efficient water distribution to crops.
Critical Components Of HDPE Pipe Extrusion Line
The HDPE pipe extrusion line consists of several key components, each playing a critical role in the efficient production of HDPE pipes:
Hopper– The starting point where raw HDPE pellets are introduced into the system.
Extruder– The core component where HDPE pellets are melted. It consists mainly of a barrel, screw, and heater.
Die Head– Attached to the extruder, it shapes the molten HDPE into a pipe form.
Vacuum Tank– Stabilizes the pipe shape using a vacuum system and cools it down to solidify its form.
Cooling Tank– Further cools the pipe to ensure strength and dimensional stability.
Haul-Off– Pulls the pipe through the line at a consistent speed to maintain uniform thickness and diameter.
Cutter– Precisely cuts the pipes to desired lengths.
How Does A Single Screw Extruder Work In HDPE Pipe Production?
The single screw extruder plays a fundamental role in HDPE pipe production, operating on a relatively straightforward principle. Here’s a detailed breakdown:
Feeding–HDPE pellets are fed into the extruder’s hopper, moving down the barrel due to gravity.
Melting–The pellets enter the barrel, where they encounter the rotating screw. Friction and heating elements along the barrel gradually melt the pellets.